3D printing has revolutionized the way we create objects, but it's not without its challenges. From failed prints to nozzle clogs, there are several common issues that can arise during the 3D printing process. In this guide, we'll explore some of the most frequent problems and provide solutions to help you troubleshoot your 3D printing issues.
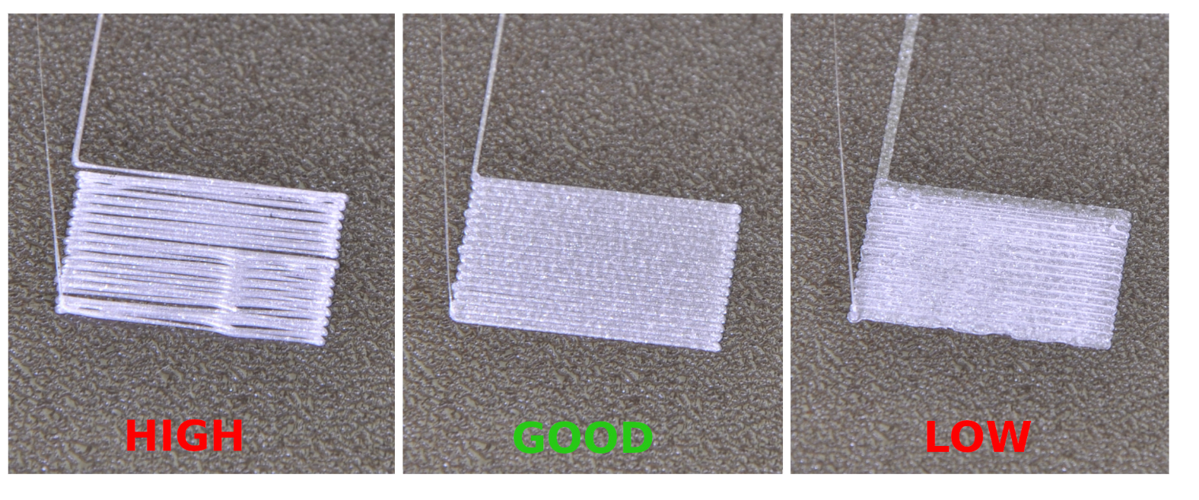
Print Quality Issues
One of the most common problems in 3D printing is poor print quality. This can manifest as layer lines, stringing, or warping. Layer lines occur when the layers of the print are not properly adhering to each other, resulting in a rough surface finish. Stringing happens when the filament oozes out of the nozzle during travel moves, leaving thin strands of plastic between the printed parts. Warping occurs when the corners of the print lift off the print bed, causing the object to deform.
To address these print quality issues, ensure that your print bed is level and properly calibrated. Additionally, adjusting the printing temperature and retraction settings can help minimize stringing. Using a heated print bed and an enclosure can also prevent warping by maintaining a consistent temperature throughout the printing process.
Nozzle Clogging
Nozzle clogging is another common problem that can disrupt the 3D printing process. This occurs when debris or partially melted filament obstructs the nozzle, preventing the smooth flow of material. As a result, the print may have gaps or under-extrusion, leading to a failed print.
To prevent and address nozzle clogging, regularly clean the nozzle and perform cold pulls to remove any accumulated debris. Adjusting the printing temperature and retraction settings can also help minimize the risk of clogs. Additionally, using high-quality filament and ensuring proper filament storage can reduce the likelihood of nozzle clogging.
Adhesion Issues
Adhesion issues, such as prints coming loose from the print bed or failing to adhere to the build surface, can be frustrating setbacks in 3D printing. This can result in warped prints, failed layers, and overall print failure.
To improve adhesion, ensure that the print bed is clean and properly leveled. Applying adhesive materials such as glue stick, hairspray, or specialized print bed adhesives can enhance the adhesion of the first layer. Using a heated print bed and adjusting the printing temperature based on the filament type can also improve adhesion and prevent warping.
Extrusion Problems
Extrusion problems, including under-extrusion and over-extrusion, can significantly impact the quality of 3D prints. Under-extrusion occurs when the printer fails to extrude the expected amount of filament, resulting in weak and incomplete prints. On the other hand, over-extrusion leads to excessive material deposition, causing the print to be overfilled and inaccurate.
To address extrusion problems, check the filament diameter and adjust the extrusion multiplier to ensure the correct amount of material is being extruded. Clearing any obstructions in the extruder and hotend, as well as calibrating the extruder steps/mm, can also help resolve extrusion issues. Additionally, adjusting the printing temperature and retraction settings can improve the flow of filament and minimize extrusion problems.
By understanding and addressing these common 3D printing problems, you can enhance the quality and reliability of your prints. Whether it's optimizing print settings, maintaining your equipment, or implementing effective troubleshooting techniques, overcoming these challenges will ultimately lead to successful 3D printing experiences.